As you can imagine, we spend a lot of time talking to facilities managers about water leak detection. And what’s their #1 bugbear? Technologies that deliver more false positives than genuine leak alerts.
What’s a false positive when it comes to water leak detection?
The simple answer is that a false positive occurs when you’re alerted to a water leak that turns out not to be a genuine, "alertable" leak.
-
It could be that a puck has detected some condensation in a water riser cupboard. Yes, it’s water - but condensation is expected near water risers. It’s not a genuine leak.
-
Some water might have been detected in an elevator shaft. Again, it’s water - but it’s pretty common in elevator shafts, so a genuine, alertable leak is when the water rises past a certain point.
-
Someone could have knocked a half-full mop bucket over and triggered a puck under appliances. Technically it’s an escape of water event - but isolated, not ongoing, and posing no further risk to the building. So it’s not a leak either.
-
Or maybe it’s a little dusty under your floors, triggering your rope sensors so they report a water leak. That’s definitely a false positive - and more common than you might expect.
Why do water leak detectors register false positives?
A lot of false positives happen because they treat water leaks as binary: water is either present, or not. But while this approach seems sensible on paper, it’s a different story when it comes to the practical applications of water leak detection.
Most places where water leaks occur will be exposed to some level of moisture that doesn’t constitute a leak - whether that’s from humidity, an occasional splash, a drip, or pooled water. And when standard water leak detectors are installed, they’ll simply detect the presence of the water, and send an emergency alert.
Facilities managers will receive alerts for these situations, investigate them, and determine that they’re not genuine leaks - just false positives.
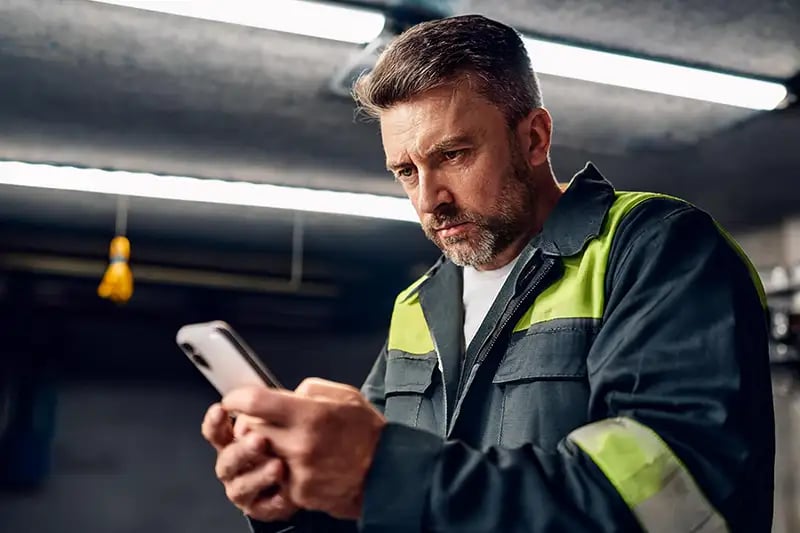
What impact do false positives have?
False positives are an expensive business for commercial and industrial owner operators.
Initially, facilities staff won’t know that they’re investigating a false positive, which means they’ll diligently respond to the alerts and inspect the leak. This will waste considerable time and resources doing so: manual inspection of each leak can be time-consuming, and out-of-hours callouts are expensive.
As the false positive rate increases, they’ll lose trust in the water leak detection solution.
First, they’ll experience alert fatigue - having received too many alerts, facilities teams will start to either ignore them, or deprioritize them. Then, they’ll experience inspection fatigue - having gone on too many callouts that weren’t genuine leaks, they’ll deprioritize or stop investigating leak alerts. While this approach will save time and effort, it runs the risk of genuine leaks not being attended to, and escalating into much larger events.
(Interested in the impact of water leaks? Check out our key water leak statistics!)
Can you eliminate false positives?
Totally eliminating false positives is a very tall order - but we’d suggest that significantly minimizing them is absolutely achievable. To do so, we need to really understand the purpose of water leak detection, understanding what constitutes a leak for facilities managers, and what a water leak alert message means for them.
For facilities managers, false positives are either leaks that don’t exist (such as when rope sensors alert and it’s dust), or leaks that are too small to necessitate any action (such as a few drops under a commercial fridge, or condensation in riser cabinets).
So to minimize false positives, each water leak detection device needs to only send a leak alert when there’s enough water to constitute what a facilities manager would consider a notifiable leak, for a specific use case, in a specific area.
Sounds straightforward enough… but it requires nuance than most standard water leak detection devices are currently capable of.
How does LAIIER minimize false positives?
At LAIIER, we know that high false positive rates undermine the perceived value of water leak detection as a whole, leaving commercial and industrial building owner-operators at risk of significantly higher water leak-related damage and downtime. So we’ve actively designed our Severn WLD water leak detector to avoid false positives:
-
We don’t take a binary approach to water detection. We know that in some instances, moisture or water will be present, without there being a genuine leak. Conversely, we know that in some instances, even a single drop of water may constitute a genuine leak that needs attention.
-
Our sensor is split into 12 segmented electrodes, each of which is capable of detecting water. This allows you to choose how many segments are wet before receiving an alert, as well as helps to build a picture of where water is present, and to gauge the size and nature of the leak.
-
We register every drop of water that pools on our sensor tape (even condensation!) and log it in our cloud-based dashboard, which gives facilities managers useful information about when water is present, and allows them to monitor smaller leaks that are not yet large enough to react to.
-
We allow facilities managers to set a leak threshold for each individual device: the number of electrodes that must be wet to trigger a leak alert. This means that leak alerts are only sent when the threshold for that specific device, in that area, is exceeded.
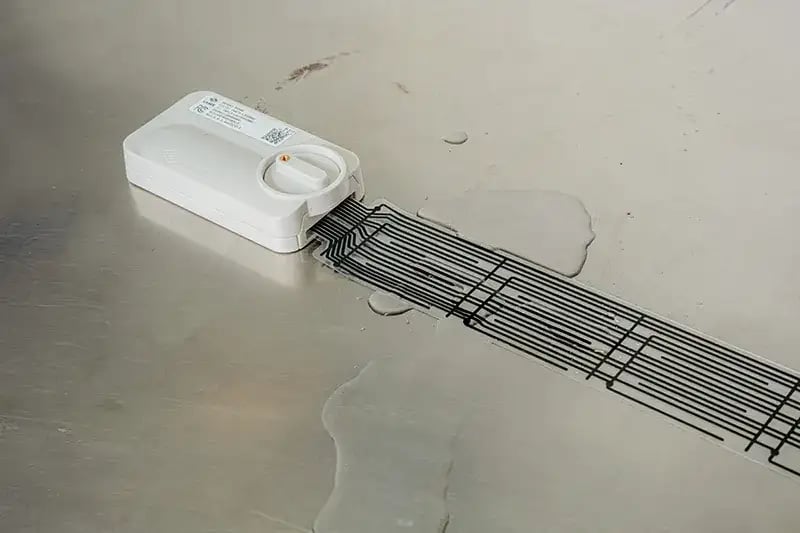
This approach means that our customers can use the same water leak detection technology to monitor very different leak sources, without worrying about false positives. For example:
-
Water typically pools in elevator shafts, but it’s important to understand when the levels start to rise too high. Facilities managers can set a threshold of 5 electrodes registering water as the point at which a leak alert should be sent.
-
In data centers, even a small water leak can cause significant damage and downtime. Facilities managers can set a threshold of 1 electrode registering water as the point when a leak alert should be sent.
-
Water leaks under sinks can cause significant damage. Facilities managers might allow 4 electrodes to register water before a leak alert is sent.
High false positive rates are avoidable
While totally eliminating false positives seems difficult, facilities managers don’t need to accept sky-high false positive rates as “standard” anymore. And in a climate when they’re increasingly being asked to do more with less, cutting back unnecessary callouts and costs due to false positives is as good for the budget as it is for team morale.
Water leak detection technology providers who truly understand the task will offer facilities managers a more nuanced view of water leaks, helping them to understand escape of water within buildings, better prioritize maintenance and repairs, and protect against damage and downtime.
Minimize false positives and increase operational efficiency in your commercial and industrial premises
Book a call with our team for a personalized consultation.