Even though printed electronics have been around since the last century, they are becoming more and more common, with the value of the printed electronics market becoming worth billions.
The idea behind printed electronics is simple: a conductive ink is deposited onto a substrate to then act as an electronic device. Most modern smartphones now include parts that were created using printed electronics. We use printed electronics to create our printed sensors.
How LAIIER’s printed sensors provide benefits
LAIIER’s sensors are also created using printed electronics; our liquid leak detection sensors are made by printing carbon ink onto a sheet of plastic, creating a resistive sensor that can detect the presence of liquids and act as a water leak sensor. Compared to conventional electronics, printed electronics have three key benefits: they are low cost, provide a high resolution and are able to cover a large area.
Additionally, by either changing the pattern that is printed onto the sensor or by changing the form factor of the sensor, it is possible to unlock different use cases. We can change the resolution of our sensors simply by changing the width of the lines that are printed; it is possible to create ultra-precise, down to 10-micron thin lines and design sensors that are highly sensitive.
A disadvantage of creating printed sensors is that the printing process can take some time to be set up, but once the setup is done, the cost of printing sensors per square meter becomes very low. Printing sensors with conductive ink instead of fabricating them conventionally also makes it very scalable to produce larger quantities, as it doesn’t take more processing to create ten meters of sensor tape or just one meter.
Comparing printed sensors to other sensors
Our sensors are acting effectively as layers within the environment, allowing us to connect to the physical environment and gather information and data. The market generally requires products to become more and more customized and printed sensors are no exception to this.
It becomes very easy to change the form factor of our sensor, from the way they adhere to the environment and surfaces down to the shape of the sensor. This is something other technologies in the field of water leak sensing aren’t able to do. Water leak sensing ropes for example are able to coil around surfaces and objects, but they can’t be of the exact same shape as pipe flanges, whereas our printed sensors can.
Another useful comparison is our printed sensors with water leak sensing pucks: the pucks are low cost and very precise, but they cannot cover a large area, whereas our printed sensors are inexpensive, provide a high resolution and are able to cover large areas.
We can also compare our printed sensors in a different field: occupancy sensing. Occupancy sensing is part of LAIIER’s product roadmap and if we were to compare our printed sensors with image sensors, printed sensors show advantages that image sensors don’t have.
Image sensors can provide high-precision data about the environment that printed sensors aren’t able to do so, but it comes at the cost of being expensive and not being able to cover a large area. On the other hand, if the image sensors are cheap, they can cover a large area but aren’t able to be as precise anymore.
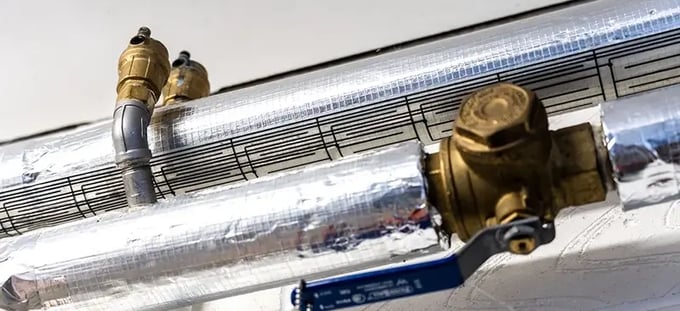
As printed electronics continue to grow and become more ubiquitous so do their functions and use cases. We are excited to be part of this growing technology trend and believe that our printed sensors are able to help businesses and industries in ways that other technology can’t.