The source of most water leakage problems in buildings (leaks that start from water within a building, as opposed to water coming from outside sources) is the infrastructure related to water supply and drainage. Think pipes, valves, fixtures, and fittings.
The good news is that most failures are relatively predictable. The bad news is that they often start in places that are difficult to see and monitor using traditional water leak detection technologies.
In this article, we'll cover the parts of your building’s water infrastructure that are prone to leaks, how they fail and leak, and which factors influence the likelihood of leaks.
Gaskets and washers
Gaskets and washers are the most common items used to prevent water leaks in a building's water infrastructure. They're used to create a water-tight seal between 2 parts of the infrastructure, which results in even water pressure throughout the plumbing fixtures, and a smooth surface to tighten nuts and bolts against.
You're probably familiar with gaskets and washers from the same role they perform on taps, shower heads, and around the drains of all the fixtures you’d find in a kitchen or washroom.
The most popular material for gaskets and washers is synthetic rubber, although you may also encounter use of silicone or a plastic compound. In places where there are high temperatures or pressures, you'll also come across gaskets and washers made of fiber and metal - for example, or a tanked hot water heater.
When gaskets and washers fail
Any gasket or washer will fail, given enough time. Rubber is particularly susceptible to deterioration, becoming brittle over time and eventually cracking. But in spite of this inevitability, predicting how long they will last is difficult, largely because so many factors influence failure, including:
- The quality of the material used in the washer or gasket.
- How often it’s used.
- The chemical attributes of the water itself.
- The water pressure.
- Temperature changes in both the water and the building.
- The quality of the installation work.
Additionally, the vibrations of water moving past washers and gaskets, and of the building itself, also have a significant effect, eventually bending or warping them so that they lose their compression seal.
Why manual inspections don't work
While gaskets and washers play a critical role in maintaining watertight seals, they're often overlooked during manual inspections, unless they're in areas that are easy to access. This creates significant risk, particularly in concealed areas; and on pipes or fixtures that operate with high water pressure and volumes, where failure could quickly result in serious flooding.
Hot water plumbing
Water heaters have a well-known lifespan of 8-12 years. The main limitation on the lifespan corrosion: over time, minerals and natural acidity in the water eat away at the steel of the holding tank, causing rust and the eventual breakdown of the tank.
To prevent this, many water heaters have a sacrificial anode, a metal rod that attracts the minerals in the water that would otherwise build up and corrode the heater walls. However, anodes typically don’t last much longer than three years; and because they're inside the tanks, the only way you can check them is by draining the heater tanks and opening them up to inspect them manually up.
To top it all off, by their nature, all parts of a building’s plumbing that heat, hold, or move hot water will experience thermal fatigue. This can be mitigated by taking measures that aim to keep the water heater and pipes at as consistent a temperature as possible, but it can’t be eliminated entirely - over time, pipes and water heaters will leak, developing cracks due to thermal stress.
Why hot water system leaks can easily be overlooked
While hot water tanks can be inspected manually, hot water pipes tend to be concealed behind drywall, making it difficult to inspect them manually. This creates additional risk for commercial building owner-operators and facilities management teams.
Pipes, valves, and joints
Predicting the lifespan of a building’s piping is difficult. While all pipes will eventually degrade, when it happens is heavily influenced by three major factors:
- The material of the pipe network.
- The chemical composition of the water.
- The design of the plumbing network in your building.
Below are the average lifespans of pipes made from the most common materials:
- Copper: 50 - 70 years, depending on usage. Will tend to spring pinhole-sized leaks as they age.
- Brass: 80 - 100 years. Brass pipes are now rarer, as lead was previously used in the metallurgy process due to its corrosion resistance.
- Galvanized steel: 80 - 100 years. The zinc coating protects against common corrosion of the pipe, but rust will take hold as the coating deteriorates.
- Cast iron: 80 - 100 years. Like galvanized steel, rust will set in as the pipe ages. Uncommon in modern buildings, you'll generally only see these in older structures, or as drain pipes.
- Polyvinyl Chloride (PVC) and similar polymer compounds: 50 - 100 years. There's less general agreement on how long these pipes will last, as PVC pipes are still relatively new, meaning we lack sufficient information to accurately predict how quickly they might degrade.
Much like water heaters, plumbing - especially metal pipes and joints - tend to deteriorate faster when used with water with high mineral content (also known as hard water). The minerals in the water build up on the insides of joints and valves, restricting water flow and causing valves to become stiff or stuck. This can lead to issues with water pressure, causing additional load and wear on the pipes.
Finally, water leaks are more likely to happen in complex plumbing systems. Joints are usually one of the spots most vulnerable to leaks due to temperature and water pressure. The more joints there are, the greater the risk.
Heating, ventilation, and air conditioning (HVAC) systems
HVAC systems leak water for a variety of different reasons.
Condensate drain clogging
One of the most common causes is clogging of the air conditioning condensate drain. This drain line runs through your building, typically made of PVC or metal, allowing condensation from the system’s evaporator coils to get out.
With a large building with a central heating and cooling system on multiple floors or where temperature control is critical, such as in a supermarket, this includes a complex system of vacuum pumps, valves and collection tanks.
If the drain line becomes clogged or a pump breaks, you’ll likely find a leak will start rapidly while the air conditioning system is running, as water backs up and overflows.
Evaporator coils freezing
Another common cause of water leaks is when evaporator coils freeze over. This may occur because air filters become clogged, or by refrigerant leaks - the latter being a much more serious concern. When either situation arises, moisture builds up around air handlers, and results in a water leak.
Why water leak detection is a challenge
While regular manual inspection and maintenance are the best way to prevent water leaks in HVAC systems, it's often impractical due to installation in concealed locations, and lack of trained staff to perform the inspections. And manual inspections aren't foolproof, so accidents do happen.
HVAC leaks tend to only be noticed when a significant leak is well underway - often to the stage of flooding. When these leaks occur, it's critical to act quickly, as HVAC systems can expel high volumes of water at in a very short period of time.
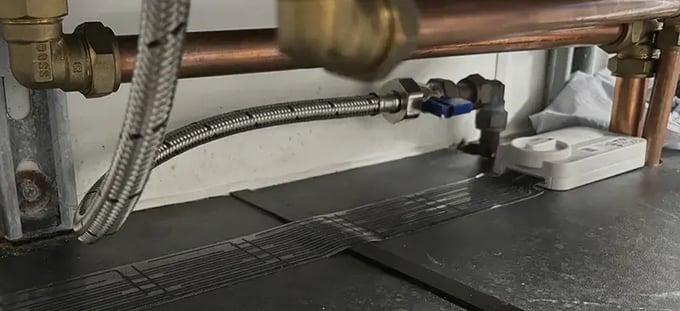
Early water leak detection is critical
Leaks in commercial and industrial buildings' water infrastructure can be hard to find, especially since the main causes are usually located behind walls or in other hard-to-reach spaces.
Armed with the knowledge that water leaks will occur - and knowing where they're most likely to occur - you're in a solid position to take steps to implement a water leak detection solution that will protect your building against damage and downtime.
LAIIER's water leak detection solution, Severn WLD™, has been designed to detect water leaks before they escalate and cause significant damage and downtime - even in concealed locations where you can't see water leaks.
Interested in understanding how Severn WLD can mitigate the damage and downtime caused by water leaks in your commercial building? See how we approach water leak detection - or book a call with our team for a no-obligation conversation.