One thing that a supermarket facility manager dreads hearing is the report of a water leak. This is because the costs can be relentless and not affordable to the average supermarket.
Costs not only include the wasted water but also the damage to the supermarket’s infrastructure, damage of spoiled goods and the resulting business downtime.
Large supermarkets can use more than 350,000 gallons of water per month - which is understandable for water-intensive appliances like refrigerator displays and HVAC systems.
However, at this scale, this makes it more likely for leaks to happen and harder for all areas to be regularly checked by staff.
Therefore, it only makes sense that supermarkets adopt predictive maintenance measures to automatically monitor their building infrastructure for water leaks.
As this article will detail, LAIIER offers the ideal water leak sensor for supermarkets that is affordable, easy-to-install and accurate.
Being fully protected with proactive measures means supermarkets can minimize costs and damage so smooth operations can be guaranteed.
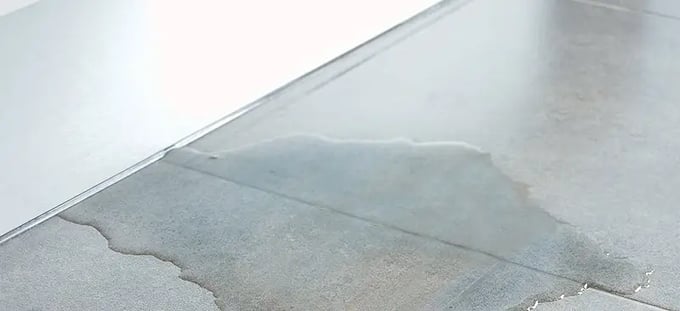
The main sources of supermarket water leaks
Leaks can originate from many places in a supermarket, however, we have identified the top three sources that have the potential to cause the most damage.
Refrigerator displays
Refrigerators and frozen food displays can consume more than 1.5 million gallons of water a year which is around half the water consumption of a supermarket. This major appliance is therefore a critical concern for supermarket facility managers.
There may be many reasons why refrigerators leak but one major concern comes from broken cooling pipes. Here, the first signs of water leaks are essential to spot as it is only a matter of hours before all the contained food has spoiled. In addition, broken door sealants and blocked drains can also cause leaks.
Subtle leaks that are not acted upon can provide conditions for mold and pest infestations that need more extensive treatment. Furthermore, leaks can be harder to detect behind and underneath refrigerators due to the narrow spaces that are usually sealed with flashing. In this situation, we, therefore, need an accurate sensor that can fit in tight spaces.
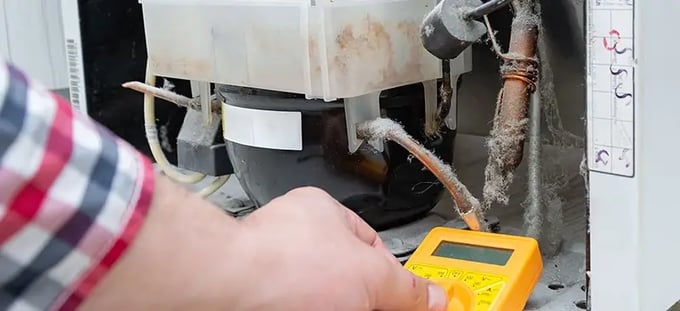
Roofing
Commercial roofs can be very problematic because of their size and is reflected by how more than US$12B is spent annually on their repair in the US. Flat roofs are a common choice for supermarkets and are particularly more prone to damage such as ponding and blistering because of drainage issues.
Depending on a supermarket's scale, the building may have HVAC systems and false ceiling tiles directly below the flat roof. These will not only obscure signs of water leaks but also water leaks can damage these critical parts of infrastructure. Additionally, water that does escape from the roof and ceiling assembly can result in wet floors which can pose increased slipping risks for customers and workers.
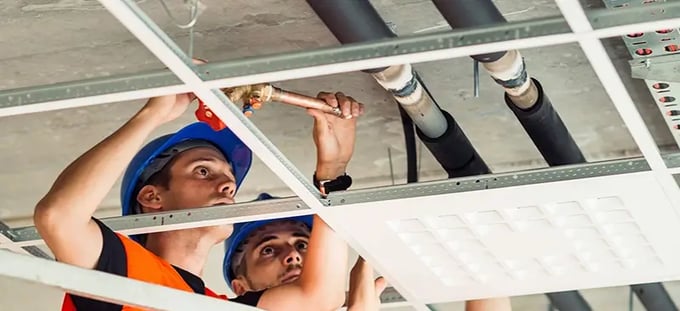
HVAC Systems
Any supermarket facility manager knows the rigor needed to keep HVAC systems operating. These pieces of equipment are essential to maintain the correct humidity, temperatures and air quality in a supermarket. With the average supermarket at around 40,000ft2, this is a huge volume of air to process.
One common type of HVAC system that uses evaporative condensers is reported to fail about six times a year. If these are not fixed immediately, they can waste more than 17,000 gallons of water per day. HVAC systems are more likely to leak due to the extreme levels of temperatures, pressures, and moisture that strain plumbing more than general water networks.
Despite the extent of damage, this damage can be easily obscured by ceiling tiles and the vast network of plumbing itself, making it less clear where the leak is coming from.
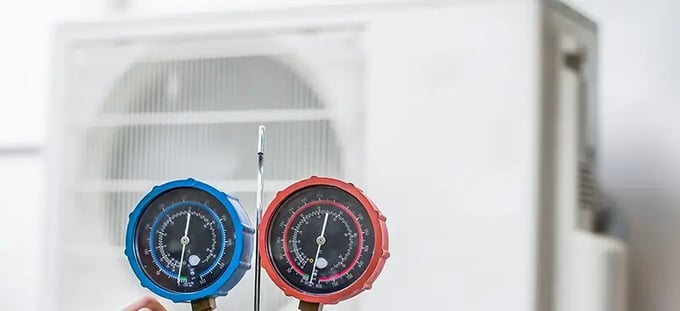
Are current inspection measures enough?
Considering water leak detection is only a fraction of a facility manager's responsibility, manual inspections at the scale of a large supermarket can be a daunting task and therefore carried out less regularly than needed. Supermarkets can sometimes hire third-party contractors for regular inspections, however, this can be a luxury that most supermarkets cannot afford due to their already tight profit margins.
Furthermore, retail facility management services are usually only called on in a reactive nature. As we explored earlier, this could already mean a whole refrigerated aisle is out-of-order so the financial damage has taken its impact. Also, servicing and repairs are only carried out if there is a significant issue. For small leaks, these are temporarily solved by catching drips in buckets and soaking spillages up with absorbent socks.
Leaks, where a gradual drip can lead to a sudden leak or worse a structural failure, would therefore only be addressed much later, missing the early window of operation to fix the leak at minimal disruption.
Consequently, supermarkets face a difficult choice of either having profits suffer from expensive facility management or saving costs by ignoring small water leaks. Both choices are not sustainable so predictive maintenance must be explored.
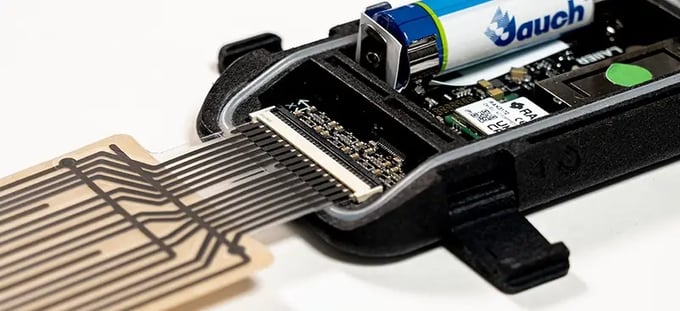
Solution for facilities managers: LAIIER
At LAIIER we have addressed these challenges of tedious water leak inspection by creating a thin, flexible water leak sensor that can be installed like a sticker to detect the first drops of a leak. The Severn WLD’s adaptable form factor is well suited to protect tight spaces such as behind refrigerators or beneath a flat roof.
LAIIER’s sticker-like sensors are also trimmable with just scissors so sensor size can be easily adjusted on-site. There are many types of HVAC systems in a single supermarket whether air curtains, rooftop units, or air handling units so sensing solutions must be adaptable to a range of equipment shapes.
Once this cost-effective solution is installed in supermarkets, facility managers and staff will be rapidly notified of any suspected leaks so action can be taken swiftly. The use of printed electronics means that a unique segmentation pattern can tell the severity of the leak, whether small, large, slowly or rapidly growing.
This data can be sent via our Surface to Cloud™ platform to a simplified user-friendly dashboard. This removes the need for expensive technicians to carry out repetitive inspections.
Learn more about Severn WLD and how to buy the devices as part of your facilities management solution.